What about the frame mounts? Would that be a good fit for a metalcloak duroflex joint? I want to build something strong yet not over build and add tons of weight.
A Primer on suspension joints:
There are 2 main styles of suspension joints currently on the market, bushings and cross axis ball joints. Others are hybrids of the main two.
RUBBER BUSHINGS:
This is the standard which all OEMs use. There are two main types, double bonded and compression.
1) Double bonded is the most common. They consist of an outer shell and an inner metal with rubber bonding the two together. In this case, the rubber is attached to the metal.
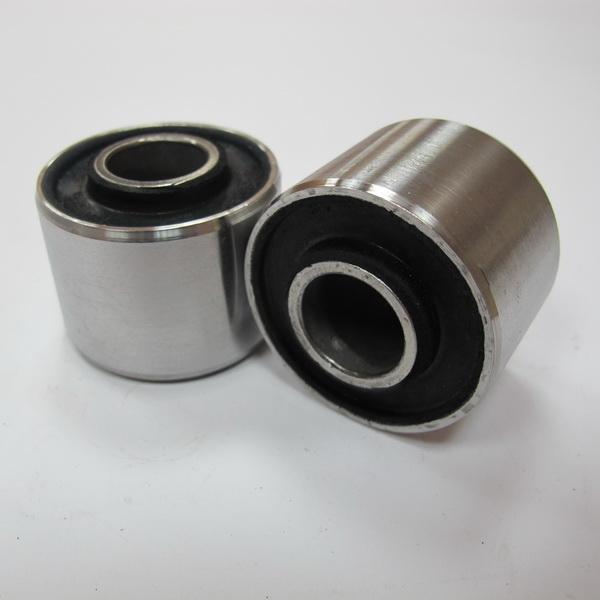
2) Compression bushings. These are a good choice for high travel suspensions and are common on Jeep JKs, TJs, Grand Cherokees, Cherokees, etc. They are non-bonded, so when over-traveled, they don't tear, they just slip. Typical construction involves molding the rubber seperate and then compressing it down and shoving it into a metal can. They utilize features to keep the bushing from walking out axially
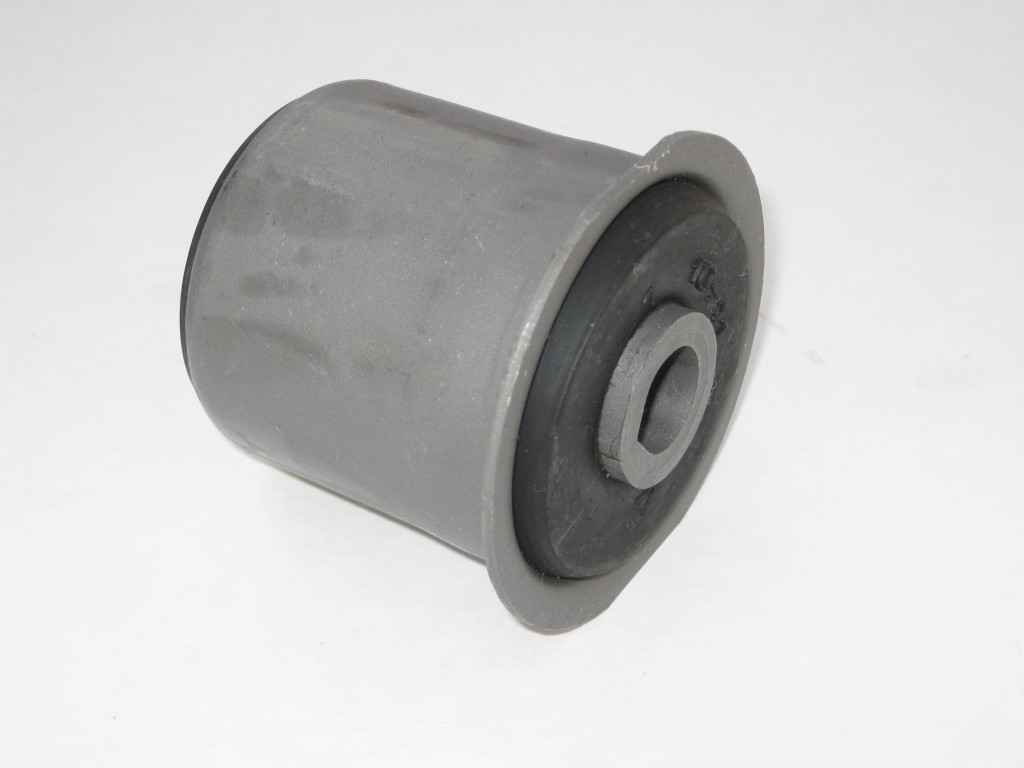
Rubber bushings are compliant in all directions, they have a spring rate in the Radial, Axial, Torsional, and Conical directions. Despite their benefits, one reason they are not common in the aftermarket is that there are few companies stateside that produce bushings and most do not cater to small run customers. China is the alternative, but quality is much lower.
CROSS AXIS BALL JOINTS
CABJs are built just like conventional ball joints with a through bolted connection. They have zero compliance in the X, Y, and Z directions, but can freely rotate in Yaw, Pitch, and Roll. (i.e. free rotation, no translation) They provide freedom of motion, but cannont absorb shock and vibration. Examples in the aftermarket would be Rubicon Express and Ballistic joints

URETHANE BUSHINGS
These fall under the bushing category. Urethane is common in the aftermarket because it is cheap and easy to manufacture. The difference is rubber behaves like a spring, it compresses and stretchs. Urethane behaves more like a liquid, when it is forced to be displaced, it doesn't compress, it moves somewhere else. This can be a very important design consideration. Additionally urethane can split easy once a crack has started.
JOHNNY JOINTS
I consider this a hybrid. They are constructed like a CABJ, but use a urethane race, so while they mostly function like a ball joint, they have some compliance like a bushing. (but not much)
METALCLOAK DUROFLEX JOINTS
I'm showing my bias here, but I saw these at Jeep Safari the same year my company unvielled our xAxis joint, and I thought these were one of the most inovative things at the show. (The
MetalCloak guys had similar thoughts about my joints)
While functionally a single-bonded compression bushing, they are shaped to allow greater roational freedom like a ball joint, but still have radial, axial, and torsional compliance like Jeep Clevite bushings. This makes them a good choice for a joint that needs high mis-alignment, but can't comprimise the benefits of a rubber bushing.
RADIUS ARM MOUNTS
It's hard to say how to construct these because there are some many factors to consider. Basically the crossbolted joint like a Johnny Joint or convention bushing would be better than the Ford radius arm bushings. The Ford design is robust for normal use, but is lacking for high travel suspensions. Brackets can be anywhere from 1/8" to 1/4" thick. For most purposes 1/8" is adaquate with 3/16" being heavy duty and 1/4" being bomb-proof. The closer the radius arm mounts are to each other on the frame side, the less bind will be induced into the axle resulting in greater flex.
RADIUS ARM CONSTRUCTION
I prefer extended radius arms to wristed ones. They are more robust and do not suffer from geometry drawbacks, but are harder to package under the truck.
To build extended arms, I like to cut off the axle end of the factory radius arms leaving ~8" of the I-beam section to attach the tube. For the extension tube, round is easy to work with but square or rectangle cross section has better bending strength for bent or relieved arms. The problem is, it's harder to bend it and bending dies are not as common. I chose 2" x .250" DOM round tube. This is heavy tube and generally overkill, however given the original length of my arms (52") I needed to be concerned about bending strength in the middle of the arm if I were to set the truck down on a rock. As it ended up, I did turtle my truck on a very large rock and there was considerable bowing of the radius arm. Luckly for me, they were still within the elastic region of their stress curve and bounced back into shape once the truck was off the rock.